When it comes to versatility, metal lathes are a perfect example. They’re must-haves for shaping, modifying and cutting metals with precision. As such, they can be used in various metal fabrication applications, from creating parts to repairing them in machinery.
What you can expect, besides the versatility and precision, are additional benefits in the likes of high-efficiency, speed, durability, longevity, ease of operation, and even cost-effectiveness. These are excellent aspects to make the most of in a range of industries that work with metals and machinery.
And, what makes lathes so useful are their distinct and useful metal lathe tools, but since there are so many types the key to getting the perfect result you expect relies on understanding them first and foremost. This is crucial to avoid any unwanted distortions, damages, or even breaking in your working pieces.
How to Identify Lathe Tools?
For the sake of making the whole process of choosing and using these tools easier, it’s best to categorise them by:
Operations
In general terms, the metal lathe tools are created to cut, shape, and finish. As such, we have the following tools based on the specific lathing operation they’re designed for:
Thread Cutting
As can be guessed by the name, these are tools meant for cutting threads on a workpiece, whether on the interior or the exterior of it. They have a nose angle, but the kind depends on the intended thread angle they’re meant for.
Chamfering
These are tools created for producing a slanting edge. This is something the turning tools can be used for too, however there’s more challenge in setting them at the right angle for this task. Once the inclination angle is high, they’re also not up to the task, as the chamfering-specific tools are.
Turning
Designed for removing the materials along the length of the workpiece they’re used on, these lathe cutting tools can reduce its diameter. Here, you can choose from two types:
- Rough – as indicated by the name, these are ideal for doing turning tasks in a single pass, and they’re not meant for creating a smooth surface, but rather a rough one that you can later finish up.
- Finishing – unlike the rough tool counterpart that removes bigger amounts of workpiece material, the finishing ones are ideal for small bits with the purpose of creating a smooth and finished surface.
Facing
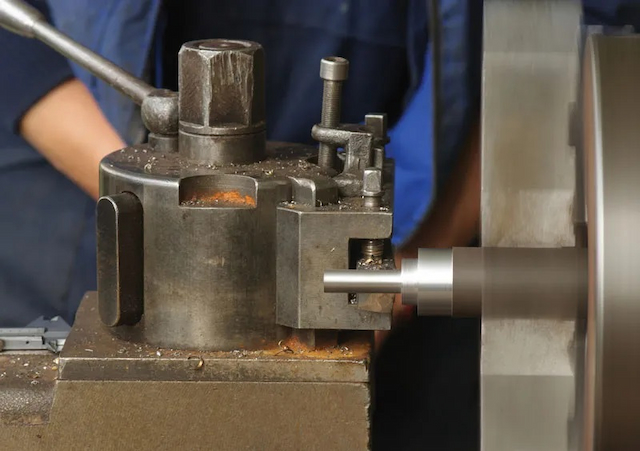
Meant for producing a smooth and level surface on the ends of the workpiece, the facing tools remove the thin layer of the working material with the side cutting edge.
Grooving
When it comes to making grooves (or narrow channels) in a piece with cylindrical surfaces, it calls for the work with grooving tools. Although there are different types, the most common ones are the square and V-shaped.
Forming
If you need to make complex shapes, then you need to use the combination of turning and grooving tools like forming. These are specialised in providing you with accurate and fast results, making them better than the mere turning tools that can be up to the task as well.
Boring
This type of lathe tool is designed for working on and increasing the diameters of holes in a workpiece. This explains the typical boring bar with cutting tool combination.
Knurling
When the task calls for making indents on a workpiece, like when you’re trying to increase the grips, then you can rely on knurling tools that are characterised by the metal rolling wheels.
Materials
The aforementioned metal lathe tools can also be differentiated by the material they’re made from, all of which are suitable and durable options. You can choose from the following:
High-Speed Steel
As indicated, high-speed tools are high-speed options, making them suitable for rough as much as semi-finish machining. Typically, they’re famous for the hardness and strength, as much as resistance to heat and wear and tear, which is understandable given this type of steel they’re made from consists of carbon, vanadium, chromium and even tungsten.
Diamond
It may not be the most affordable option there is, but if you can invest in diamond lathe tools, then go for it because it’s known for being very hard and fit for work with various materials.
Cubic Boron Nitride
Another hard alternative, the cubic boron nitride tools are durable, and are fit for rough machining even on materials like cast iron.
Ceramic
Don’t let the thought of ceramic as a fragile material fool you. On the contrary, this is a very hard and wear-resistant choice perfect for finishing work on hard materials.
Cobalt
When it comes to tools fit for heavy-duty applications, look for cobalt’s hardness and heat-resistance.
Carbide
This is yet another high-end option that’s not among the most affordable, but it’s strong and fit for work with various materials. In terms of strength, it’s even stronger than HSS, making it perfect for high-speed operations with tough materials like stainless steel.